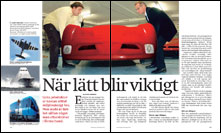
När lätt blir viktigt
En lättare bil ger många vinster. Den drar mindre bensin, sliter mindre på vägbanan, bullrar mindre, har bättre prestanda och rymmer mer last. Men ändå är det inte lägre vikt som lockar biltillverkarna när de funderar på att bygga i lättare material.
I ett projekt som pågår vid Kungl. Tekniska Högskolan, KTH, räknar forskarna på en ny bottenplatta till ett tyskt bilföretag. Den lastbärande strukturen i bilen ska vara av kolfiberkomposit, och målet är att den ska vara mindre än hälften så tung som motsvarande struktur i stål. En radikal minskning ner till 80 kilo, i stället för 200 kilo. Men ändå är viktminskningen inte skälet till att man skapar den nya strukturen.
Det som lönar sig är att den nya bottenplattan består av betydligt färre delar. En stålstruktur omfattar 200 delar, och varje del kostar i inköp, lager, hantering, montering och testning. Den nya kompositstrukturen kommer att bestå av färre än 60 delar.
– Bara vikt biter inte på bilindustrin, säger Dan Zenkert, professor i lättkonstruktioner på KTH.
I de fall bilarna skulle bli lättare med nya material fylls de ofta ändå med nya finesser som tynger.
Större vagn viktigare
I Stockholms tunnelbana rullar sedan i somras en annorlunda tunnelbanevagn. En helt ny lättviktskonstruktion. För passagerarna märks den nog mest just på sommaren genom att den har en förbättrad klimatanläggning ombord. Tittar man noga ser man att den har slät plåt, i stället för korrugerad, på vagnssidorna. Invändigt kan man också märka att den känns litet rymligare.
Vagnen är i själva verket hela 2 decimeter bredare invändigt. Mittgången är cirka 30 procent bredare, och teoretiskt ryms det därför 35 extra personer i vagnen. Detta tack vare ett nytt tunnare men självbärande material som består av ett knappa millimetern tunt skikt med rostfritt stål, därefter en plastfyllning och så ytterligare ett – ännu tunnare – inre rostfritt skikt. Med detta nya finurliga material kan man bygga vagnens bärande stomme, isolering och ytskikt i ett och samma moment. Materialet är visserligen dyrare än det konventionella, men det sparar man in på minskad materialåtgång och framför allt enklare montering.
– Vagnen är lättare än den vanliga vagn 2000 som sedan 1998 trafikerar underjorden i Stockholm. Vikten per passagerare är 10 procent lägre än hos en konventionell vagn, berättar Lennart Nilsson på Bombardier, som tillsammans med bland andra KTH har konstruerat den nya vagnen.
Slät yta viktigast
Men den minskade energiåtgången eller möjligheten till litet bättre prestanda är inte det avgörande. Det är däremot möjligheten att få in fler passagerare och att passagerarna upplever vagnen som mer komfortabel.
Korvetten Visby, den första i sitt slag i världen, är ett militärfartyg på 73 meter helt byggd i kolfiberkomposit (bild 1). Den är betydligt lättare än vad motsvarande båt i stål skulle vara. Lätt och därmed snabb och smidig, driftsnål och miljövänlig. Men skälet till valet av byggmaterial var ursprungligen något annat:
– Det krävdes en perfekt slät yta. Plåtbåtar blir buckliga, både när de tillverkas och när de används. Bucklorna är som parabolantenner för radarvågor, berättar Anders Lönnö, projektledare vid Försvarets materielverk, som just nu provar den nya korvetten.
Den ultramoderna båten är ett så kallat smygfartyg. Det ska ta sig fram praktiskt taget osynligt för fiendens radar. Radar bygger på att man sänder ut en radarstråle mot ett föremål och mäter reflexen. Smygteknik går ut på att avlänka eller absorbera radarstrålen så att den inte lämnar några reflexer. Den kolfiberarmerade plast som Visby är byggd av är utmärkt genom att den är helt slät, och därigenom på ett kontrollerat sätt reflekterar i önskade vinklar.
– Att skrovet är lättare är givetvis en jättefördel, men steget till kolfiber har också inneburit många andra fördelar, säger Anders Lönnö.
Det avancerade skrovmaterialet gör att skeppet inte ger ifrån sig någon värmestrålning, vilket i sin tur gör det osynligt för värmesensorer. Kolfibern är också elektriskt ledande, vilket gör att den fungerar som avskärmning för elektromagnetisk strålning. Skrovmaterialet är dessutom omagnetiskt.
Korvetten Visby är byggd i så kallad FRP-sandwich: två tunna skal av kolfiberarmerad plast samt hård men lätt cellplast däremellan. Skrovmaterialet byggs på plats med hjälp av vakuuminjicering, vilket innebär att den flytande plasten fördelas i kolfibermattan när luften sugits ut. Det är en relativt ny teknik som ger extrem släthet och garanterar hög och jämn kvalitet.
Man kan tro att ett oprövat och relativt manuellt arbete som detta borde bli dyrare än konventionell teknik. Anders Lönnö menar att det visserligen är svårt att jämföra, men troligen är fartyget billigare, eller åtminstone inte dyrare än ett stålfartyg med motsvarande prestanda.
Ändå har det nya lätta materialet svårt att slå sig in på den civila marknaden.
– Det har förbryllat oss, säger Anders Lönnö. Passagerarfartyg och fraktfartyg byggs fortfarande genomgående av stål.
Detta trots att vikten, särskilt på kryssnings- och passagerarfartyg, spelar stor roll för fartygets prestanda och sjövärdighet. Särskilt för höga fartyg spelar vikten på de översta våningarna mycket stor roll.
Ett viktigt skäl till motståndet är att de nya materialen inte är brandsäkra. Både glasfiberarmerad och kolfiberarmerad plast brinner. När det gäller korvetten Visby har man löst problemet med särskild isolering, med färg som sväller och med ytterligare system som tillsammans ser till att båten uppfyller internationella krav på brandsäkerhet till sjöss.
Metallskum märkligt material
Bilindustrin är minst lika konservativ som varvsindustrin, trots att brandsäkerheten här inte är ett argument.
– Bilindustrin har genom åren investerat enorma summor i pressverktyg, och därför går man ogärna över till andra produktionsmetoder, berättar Dan Zenkert.
De avancerade pressverktygen kan dock antagligen användas med smärre modifikationer till ett nytt material som Dan Zenkert hoppas mycket på: metallskum.
Metallskum är det märkliga material som uppstår när flytande aluminium under en speciell process blandas med gas precis när det ska till att stelna.
Än finns materialet inte i några tillämpningar, men förhoppningarna är stora. Ett användningsområde är som utfyllnad mellan två lager av tunn aluminiumplåt. Ett sådant material passar de tillverkningsmetoder som används i bilindustrin.
– Man bygger redan i dag bilar helt av aluminium. Att använda tunnare aluminiumplåt med aluminiumskum emellan skulle ge lättare och styvare konstruktioner. Man skulle också kunna fylla diverse balkar med skum och på så sätt kraftigt öka energiupptagningsförmågan, vilket förbättrar bilarnas krockskydd, berättar Dan Zenkert.
Kompositer i bilar
I bilar som tillverkas i få exemplar är plastkompositerna redan i dag helt dominerande. När man bygger en extremt lätt bil, som den italiensk-svenska Bebi, sker det med kompositer (bild 1). Så blir det också en bil som väger under 400 kilo och som får häpnadsväckande prestanda, som 0-100 km/tim på blotta 3,6 sekunder.
Kompositer är i sig inget nytt. Förhistoriska hus, byggda med lera och pinnar, består av inget annat än kompositmaterial: det sammanslagna materialet har betydligt bättre egenskaper än något av de två ingående materialen var för sig.
På 1950-talet uppfanns glasfiberkompositerna. Man hade upptäckt att fibrer av glas har egenskaper som skiljer sig från glasets, genom att de är böjliga, men samtidigt likt glas mycket styva. Blandas glasfibern med plast får man ett lätt och starkt material.
Ännu finare egenskaper har kompositer armerade med kolfibrer. De blir lättare och starkare än motsvarande glasfiberkompositer. De har dessutom andra egenskaper, som att de är elektriskt ledande och ogenomskinliga. Det är av kolfiberplast som korvetten Visby är byggd, liksom bottenplattan i den tyska personbilen.
– Det kan tyckas enkelt, men inga andra material slår kolfibern, och det är märkligt att tänka sig att detta är samma material som den grafit som är så mjuk att den används i blyertspennor, säger Rodney Rychwalski, materialforskare vid Chalmers tekniska högskola.
Ett problem med kolfiber har varit det höga priset. Men tumregeln är att priset halveras vart sjunde år.
– Tillsammans med andra nya fibrer, som aramid och nylon, har kolfibern nu stulit showen från glasfibern, säger Rodney Rychwalski.
När Ferrari bygger bilar av plast är det aramidtrådar blandade med kolfibrer som ger dem dess lätta och samtidigt kraschtåliga hölje.
Nanokompositer
Det som Rodney Rychwalski forskar på är dock efterföljaren till dessa fibrer: nanokompositer. Det är material med trådar i storleksordningen en tusendel av dem som finns i kolfiberkompositerna. Vi talar nu om trådar som är hälften så tjocka som DNA-molekyler. Det går 60 000 sådana rör av kolatomer, nanorör, på ett enda hårstrå.
Så sent som år 1991 publicerades den första vetenskapliga artikeln som på allvar beskriver de fantastiska egenskaperna hos nanorör. Artikeln satte i gång ett intensivt forskande om nanorörens egenskaper och möjligheter.
Man mäter styrkan hos olika trådar med hur hårt man kan dra i dem innan de går av. Vanlig kolfiber är tio gånger så stark som glasfiber, och nanorören kan vara upp till hundra gånger starkare än kolfiber!
Nanorören ger material som alltså är extremt styva och starka. De har dessutom fantastiska värmeegenskaper och är elektriskt ledande. Det räcker med att en plast förstärks med 2 promille nanorör för att den ska bli elektriskt ledande. Detta ska jämföras med att mer än tio gånger så mycket kolfiber behövs för att uppnå samma effekt.
De första produkterna finns redan, men tystnadsavtal håller de flesta hemliga, säger Rodney Rychwalski. Det finns ett antal tillverkare i USA och Japan. För mindre än ett år sedan var priset omkring 500 kronor per gram nanorör, i dag är det nere i 15 kronor per gram.
Kompositer för miljön
Växtfiberforskarna är på väg ner till samma nivå som Rodney Rychwalski, nanoområdet.
Just nu sker en intressant utveckling inom så kallade biokompositer. Forskarna har börjat hitta metoder för att tillverka material där de ingående delarna kommer från växtriket, är biologiskt nedbrytbara och har mycket goda mekaniska egenskaper, nästan i klass med glasfiber.
Traditionella kompositmaterial görs av oljebaserade kemikalier. För att en komposit ska bli ekologisk måste dels fibrerna vara av naturmaterial, dels den plast som håller samman fibrerna härstamma från förnybart material.
För att göra plastkompositerna så styva och starka som möjligt tittar man på växtfibrernas beståndsdelar. Den minsta tråddelen i en växtfiber är den så kallade fibrillen.
– För att utveckla materialen ytterligare har vi nu börjat arbeta med mycket små delar av fibern, nere på molekylnivå, och använder alltså inte hela växtfibern, säger Lars Berglund vid Biofibre Materials Centre vid KTH.
Men än är det många svåra problem kvar att lösa. Fibrerna och plasten som de ska armera vill inte riktigt samarbeta.
– Vi måste antingen manipulera fibrillerna eller göra något åt plasten, antagligen både och, säger Lars Berglund.
Lätt ett eget argument
Det första område där nanokompositer kan komma att användas är antagligen i rymden eller i vissa sporter med extrema materialkrav, som seglingstävlingen America’s Cup. Andra områden, som inte är så priskänsliga och där vikt i sig är ett argument, är militärflyget. De nya materialen och konstruktionerna letar sig sedan via det civila flyget in i alla möjliga tillämpningar.
Vid sidan om flyget är det på andra håll inom transportindustrin som man kan göra direkta vinster på viktminskning. Hans Hansson, vd på Sicomp i Piteå, ett industriellt forskningsinstitut som specialiserar sig på kompositer, plast och gummi, tar en ny lätt trailer som exempel:
– Många varor som transporteras i långtradare är för tunga för att lastas så att de fyller trailern till brädden.
Mer mjölk i lastbilen
Det gäller till exempel mjölk. För varje kilo man sparar på trailern, kan ytterligare ett paket mjölk lastas. Vid Sicomp har man därför utvecklat en kyltrailer som genom att byggas av plast är ett ton lättare än en konventionell trailer. Hans Hansson räknar upp alla som tjänar på den nya konstruktionen.
– I första hand är det förstås åkaren. Med en trailer som är 15 till 20 procent lättare spar han in nästan var femte tur.
– Men också samhället tjänar i form av mindre slitage på vägarna, mindre trängsel och mindre utsläpp. Och i slutändan gynnas säkert också konsumenten, när priserna på frakterna minskar.
Även vid de turer där varorna redan i dag fyller hela trailern spelar den mindre vikten roll. Bränsleförbrukningen minskar med omkring 7 procent, tack vare trailerns lägre vikt.
Men till och med när forskarna har lägre vikt som primärt mål visar det sig ibland att kunderna värdesätter andra egenskaper i de nya konstruktionerna. Vid Sicomp har man sålunda utvecklat en ny container av glasfiber. Den är 28 procent lättare än en konventionell container av stål. För kunderna var det dock den betydligt bättre hållfastheten som blev avgörande när den nya containern skulle marknadsföras. Den har dessutom bättre värmeisolerande egenskaper.
För miljöns skull
När vikten i sig är en drivkraft är skälet numera ofta miljövinster. Ett lättare material kanske inte försvarar sitt högre pris enbart genom minskade transportkostnader, men om det dessutom är mer miljövänligt, är det ytterligare ett skäl för företagen att välja lätt.
– Lätta produkter är nästan alltid miljömässigt bra, säger Anders Marén på Verket för innovationssystem, Vinnova. Han handlägger just nu ett program om lätta material och lättviktskonstruktioner och menar att miljön seglat upp som en av de viktigaste drivkrafterna.
– Det är ett tacksamt område, så länge man är vaksam på att de ingående materialen inte i sig är miljöbelastande eller sammansatta på ett sådant sätt återvinning blir omöjlig, avslutar han.
Plastbro kan lyftas på plats
En konventionell bro skulle vägt omkring 100 ton. Den här nyskapelsen av prefabricerade glasfiberbalkar väger bara 38 ton.
Materialkostnaden är högre för en kompositbro, men installationskostnaden är väsentligt lägre eftersom arbetstiden är kortare – 3 veckor i stället för 6.
Flygplan i trä
Det var inom flyget som sandwichkonstruktioner användes första gången. Flygplanstillverkaren de Havilland utvecklade under andra världskriget ett extremt lätt och snabbt flygplan kallat Mosquito. I strid med den rådande trenden byggdes planet av trä och inte aluminium. För att ändå få en tillräckligt stark men fortfarande lätt flygplanskropp limmades träfaner på båda sidor av en kärna av balsaträ. Därmed var den första sandwichkonstruktionen född.
Mosquiton blev tack vare sin låga vikt och sina starka motorer det dittills snabbaste bombplanet. Som så ofta vid viktminskning fanns också en eftertraktad bieffekt. Trä var till skillnad från aluminium inte en bristvara, och snickare fanns det fler att tillgå än hantverkare kunniga i aluminiumsvetsning.