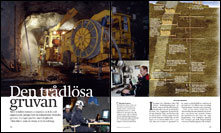
Den trådlösa gruvan
I ett plan över Atlanten sitter Ulf Olsson, forskningsingenjör på LKAB. Han är på väg till en forskningskonferens om gruvteknik i Tucson, USA. Flygplanet är modernt, så han kopplar upp sin bärbara dator till internet. Sedan loggar han in på LKAB i Kiruna och får upp en bild tagen av en borrmaskin nere i gruvan. Men det är inte ett gammalt foto, utan en direktbild av vad borren gör just nu. De siffror som samtidigt visas kommer från borrens sensorer.
Från 10 000 meters höjd kan Ulf Olsson följa borrmaskinen via internet 1 000 meter ner i gruvan. Senare på konferensen gör han om uppkopplingen och publiken häpnar. Ett exempel på unik högteknologi och en av förklaringarna till att Kirunagruvan i dag är extremt lönsam. År 2004 var LKAB:s vinst 2 miljarder kronor. Omsättningen var 9 miljarder kronor.
Kina höjer priset
Den kanske viktigaste orsaken till den goda lönsamheten är den höga efterfrågan på järnmalm. Just nu är priset sensationellt högt. Främst är det den stora efterfrågan från Kina som driver upp priset, men också i andra delar av världen har efterfrågan på järnmalm varit större än tillgången.
– Vi upplever en extremt kraftfull råvaruboom, säger Marian Radetzki, professor i nationalekonomi och expert på råvarumarknader.
För femton år sedan såg det annorlunda ut. Och då dömdes LKAB ut:
– Den ligger för långt bort, är för liten, malmen ligger för djupt och är inte rik. Det är svårt i förhållande till Brasilien och Australien. Där har man landskap av järnmalm, sa Marian Radetzki då.
Nu har han ändrat sig.
– När jag förstod vilken fördel LKAB drar av att man har magnetitmalm ändrade jag min syn, säger han.
Den vanligaste järnmalmen i världen heter hematit. Men i Sverige, Norge och Ryssland finns det magnetit, en malm med två goda egenskaper. Den är magnetisk och därför lättare att skilja ut från gråstenen, och den avger värme när man tillverkar så kallade järnpellets, vilket gör att förädlingen blir billigare än med hematit. I dag säljs 70 procent av LKAB:s järnmalm i form av runda brända järnkulor – pellets – och man siktar på att nå upp till 100 procent.
Kunden vill ha pellets
De senaste femton åren har LKAB medvetet satsat stora resurser på förädlingssteget, det som händer med malmen sedan den kommit upp ur gruvan. Man har blivit betydligt bättre på att leverera det kunderna vill ha. Lennart Widenfalk, biträdande professor i ekonomisk geologi vid Luleå tekniska universitet, anser att detta är ett viktigt skäl till att LKAB lyckas så bra.
– Jag tycker att Marian Radetzki underskattade kraften i forskning och utveckling, säger Lennart Widenfalk. Numera får varje kund i princip en egen produkt.
För att veta exakt vad kunderna vill ha byggde LKAB för åtta år sedan en experimentmasugn i Luleå. Den är fortfarande den enda i sitt slag i världen, och här kan man efterlikna processerna hos de olika kunderna och därmed se till att dessa får så bra och anpassade pellets som möjligt. Kunderna, det vill säga stålindustrin, köper järnpellets uteslutande för att smälta dem i sina masugnar.
Nu inriktas utvecklingsarbetet på att dels ytterligare effektivisera pelletsproduktionen, dels tillverka järnkulor med så jämn kvalitet som möjligt.
Allt färre under jord
LKAB gör alltså rekordöverskott på grund av ett högt råvarupris, att man har rätt malm och att man anpassat sig till kunderna. Men det finns även en fjärde förklaring, och den handlar om automatisering och rationalisering. På femton år har personalen halverats, med oförändrad produktivitet.
Numera är det rätt öde i gruvan. Det är kanske också det mest slående intrycket när jag själv gör ett besök i Kiruna. Vägen ner i gruvan är jämn och rak. Ingen mötande trafik, men tunneln är så bred att möten är möjliga. Vi färdas i en vanlig liten transportbuss. Backen är inte brant, men när det slår lock för öronen förstår jag att vi kommit en bra bit ner. Markeringar på gruvgångar som vi far förbi berättar att vi är på 500-metersnivån, 600-metersnivån och 700-metersnivån. Vi är på väg till en nivå som ligger 1 000 meter under gruvbergets topp.
Bussen lämnar den asfalterade vägen och svänger in i ett produktionsområde. Det finns 40 mil asfalterade vägar inne i Kirunagruvan. De används främst för transporter av människor och maskiner som ska upp och ner i gruvan. I det produktionsområde vi kommer till borras det just nu. Senare ska här sprängas och brytas malm. De enda människor jag ser är en grupp studenter.
Den som styr borren sitter i ett bergrum på 775-metersnivån. Egentligen skulle operatören kunna sitta i ett kontorshus ovan jord. Kan man koppla upp sig mot riggen från ett flygplan på 10 000 meters höjd, går det givetvis att styra den från ett hus någon kilometer bort. Att så inte sker i dag beror dels på att den som borrar ibland behöver flytta maskinen, vilket ännu inte kan göras med fjärrstyrning, dels på att de anställda värnar om de extra lönetillägg man får om man arbetar under jord.
Det finns flera skäl till att andra gruvor inte har drivit automationen lika långt, men det viktigaste är antagligen att det är för dyrt. Om gruvarbetarlönerna är låga är det inte lika lönsamt att ersätta arbetskraft med automatik. När Ulf Olsson nyligen visade systemet på konferensen i Tucson var dock publiken mer intresserad än tidigare. Anledningen till det nyvaknade intresset är att en borrigg som är uppkopplad mot företagets nätverk kan ge värdefull information om berget, brytningen och borren. Informationen kan användas bland annat i bearbetning av malmen och vid service av borren.
Mera fjärrstyrt
De operatörer som styr lastmaskinerna efter att man sprängt, sitter i kontorshuset på sjunde våningen i LKAB:s kontorshus. Operatörsgränssnittet är så automatiskt att en förare kan köra två maskiner samtidigt! Lastningsprocessen är halvautomatisk, vilket innebär att operatören fyller skopan varefter maskinen själv åker i väg och tömmer massorna. Maskinen lastar normalt 25 ton åt gången i skopan.
Klockan två varje natt spränger man. Då får ingen vistas i gruvan. Både tryckvågen och gaserna är dödande. Efter sprängning vädras gruvan. Så fort dammet lagt sig, kan de fjärrstyrda lastmaskinerna sätta i gång. Det dröjer ytterligare några timmar innan människor kan gå ner.
Wlan är för komplicerat
Både borren och lastmaskinerna styrs via trådlös kommunikation. Tekniken fungerar bra men är begränsad eftersom den inte följer någon öppen standard. På ett kontor är det närmast självklart att man väljer dator från en tillverkare, program från någon annan och skrivare från en tredje. I processindustrin är det fortfarande ofta en tillverkare som levererar hela paketet. Utvecklingen går dock mot standardlösningar även här. Enligt Ulf Olsson kommer man att försöka välja ett standardiserat kommunikationssystem nästa gång. Det blir billigare, eftersom produktutvecklingen är snabbare och konkurrensen mellan leverantörerna är större. Den största vinsten med att välja standardsystem är dock att man lättare kan påverka och använda den information som skickas mellan maskinerna.
Studenterna som jag möter nere i gruvan mäter på en sådan standardteknik, i detta fall ett trådlöst nät. Tidigare har man prövat med samma teknik som används i de flesta hem och kontor i dag, som säljs under namn som wi-fi och Airport. Utvecklingen av denna teknik har varit intensiv de senaste åren, och just nu provar man om tekniken fungerar bra i gruvan. Resultaten är bättre än väntat. Trots höga frekvenser och låg effekt erhålls god täckning i gruvan.
Lyckosamt breda
Att vägen ner i Kirunagruvan känns bred och stor är inte en tillfällighet. Jämfört med andra länder är orter och gångar bredare i Sverige. Systemet med tvärbanor, tunnlar där man kan köra ner i gruvan även med stora fordon, är också ovanligt i andra länder. Men med högre produktionstakt och större maskiner har det visat sig vara lyckosamt. På andra håll får man ta isär maskinerna uppe på markytan, skicka ner dem och sedan sätta ihop dem på plats nere i gruvan.
Men även om vägarna ner i Kirunagruvan är breda och asfalterade tar det tid att få ner en reservdel till 1 000-metersinvån. Och än mer trafikproblem har man i trånga och djupa gruvor, som kolgruvorna i Tyskland.
Ett skäl till de breda svenska tunnlarna är traditionen. Men viktigare är kanske att gruvorna har lång livslängd. I Kirunagruvan räknar man med att kunna bryta järnmalm i ytterligare 200 år. Det betyder att det lönar sig att investera i infrastrukturen.
Ständig ombyggnad
Ändå är gruvan en fabrik som ständigt byggs om. Det gäller att ha så små kostnader för infrastruktur som möjligt. En del av automationen har dock ökat behoven av infrastruktur, och nu försöker man åter minska den. I dag dras till exempel ledningar för el, tele och flera olika kablar för data till centrala punkter. Ut i de lokala orterna drar man sedan de kablar som är nödvändiga för maskinerna. Forskningen på kommunikation i gruvan syftar förstås till att minska antalet kablar.
De automatiska lastmaskinerna måste också ha ett stort antal noggrant inmätta reflektorer som referenssystem när de ska navigera i tunneln. Reflektorerna hittas av roterande lasrar som sitter på lastmaskinerna. Det är dyrt men är det enda system man hittills har prövat där lastmaskinerna kan navigera med tillräcklig noggrannhet i hastigheter upp till 25 kilometer i timmen.
Det finns även andra metoder för navigering i underjordsgruvor. De baseras på avståndsmätning kombinerat med så kallad tröghetsnavigering, maskinen kan alltså själv räkna ut hur långt den har förflyttat sig sedan den senast mätte sin position exakt. Tidigare tester har visat att tröghetsnavigeringen inte varit tillräckligt noggrann. Ett visst mått av tröghetsnavigering betyder att man kan minska antalet reflektorer och därmed kostnaderna för infrastrukturen i gruvan.
Möjligen kan man också hitta smartare rutter för lastmaskinerna. I ett forskningsprojekt räknar matematiker på den smartaste körvägen för truckarna mellan den plats där de hämtar malmen och schaktet där de tömmer den. De räknar också på om det kan gå att ta kurvorna litet snabbare och därmed öka produktiviteten ytterligare.
– Vi har indikatorer på att det ska kunna gå 5 procent snabbare, vilket betyder tiotals miljoner kronor per år, säger Per-Olof Samskog, som är ansvarig för strategiska FoU-projekt inom LKAB och dessutom adjungerad professor vid Luleå tekniska universitet.
Var är de?
Nu åker vi runt och letar efter en av dessa automatiska lastmaskiner. Men gruvan är stor och öde. Vi möter några underhållsarbetare som berättar var närmaste lastning sker. Vi irrar runt en stund i labyrinten av gångar för att hitta dit. Men utan framgång.
Det slår lock för öronen när vi åter tar oss upp till marknivån. Det är ljust men disigt ute. Gruvarbetarna som sitter på sjunde våningen i kontorshuset konstaterar att det väl inte är mycket att se, när jag frågar om de uppskattar att ha kommit upp ur gruvan.
Kina driver upp priset
Stålproduktionen i världen passerade år 2004 för första gången en miljard ton. En tredjedel, drygt 300 miljoner ton, står Kina för. Men även i Europa och Japan har ståltillverkningen och därmed efterfrågan på järnmalm växt, om än blygsammare.
Tillväxten gör att världshandeln med järnmalm ökar och priset stiger. Inte bara råvarupriset stiger utan också priset på sjötransporterna som är en relativt stor del av det totala kostnaden för järnmalm. Medan Kina i första hand köper inhemsk järnmalm och malm från Australien och Indien, köper Europa från Sverige. LKAB:s kunder i Europa, Mellanöstern och Nordafrika efterfrågar nu mer järnmalm än företaget kan leverera.
Produktion av järnmalm i världen 2004 (miljoner ton)
- Kina 280
- Australien 220
- Brasilien 220
- Indien 110
- Ryssland 95
- Ukraina 66
- USA 54
- Sydafrika 40
- Kanada 31
- Sverige 22
Totalt 1 250
Berget smäller
Gruvan i Kiruna är 1 045 meter som djupast, mätt från gruvbergets topp. Malmen på den nivån beräknas räcka till år 2018.
Det finns gruvor som är både 2 000 och 3 000 meter djupa. Problemet med större djup är framför allt att trycket i berget är större. Det innebär att underjordskonstruktionerna utsätts för allt högre belastning och att risken för ras ökar. När spänningarna ökar får man också problem med så kallat smällberg, det vill säga att berget helt enkelt exploderar.
– På riktigt stora djup får man tendenser till jordbävningar som orsakas av brytningen, berättar Erling Nordlund, professor i bergmekanik vid Luleå tekniska universitet.
Forskningen inom bergmekanik behandlar bland annat bergets hållfasthet, beskrivning av, som man säger, hur berget går i brott och hur berget ska förstärkas för att ge stabila förhållanden. Ju mer man vet om hur berget beter sig, desto bättre kan man planera infrastrukturen i gruvan och brytningen.
Malmförädling med fler datorer
I gruvan bryts malm som sedan krossas, mals, separeras, rullas och sintras. Malmen som bryts ser dock olika ut, har olika sammansättning och beter sig olika när den bearbetas. Det gäller att utifrån detta få en maximal produktion med så jämn kvalitet som möjligt.
För att lyckas med det måste man mäta och sedan modellera och styra processen utifrån dessa modeller.
– Vi mäter på sexton olika parametrar inne i kvarnen, säger Per-Olof Samskog, som är ansvarig för strategiska FoU-projekt inom LKAB och adjungerad professor vid Luleå tekniska universitet.
Men det räcker inte. Fortfarande är det stora delar av processen som fungerar som en svart låda – man vet inte vad som händer inne i maskinerna, bara vad som går in och vad som kommer ut. Per-Olof Samskog behöver mäta mer och noggrannare.
Överst på önskelistan finns beröringsfri mätning som klarar tuffa miljöer. Tillsammans med flera andra processindustrier i norra Sverige har man startat ett projekt som heter Process-IT Innovations. Satsningen är unik eftersom flera olika processindustrier deltar, som gruv-, stål- och pappersindustri. Och eftersom den går hela vägen från råvara till färdig produkt.
Att man kan samverka mellan olika processindustriföretag i Sverige är kanske inte så märkligt, de konkurrerar ju inte. Men gruvindustrin är global och man träffas gärna och utbyter erfarenheter.
– Vi är en internationell bransch med mycket utvecklingssamarbete mellan gruvföretagen. Vi orkar inte heller alltid driva utvecklingsprojekten själva, säger Per-Olof Samskog.
Mäter kulor
I ett delprojekt prövar man till exempel att mäta storleken på kulorna av järn som ska brännas till pellets. Deras form och storlek påverkar i hög grad processen i stålverkens masugnar.
Med hjälp av tredimensionell kamerateknik kan man nu avbilda kulorna där de kommer rullande. Avancerad bildanalys ger sedan värden som kan användas för att modellera och styra processen. Tekniken bygger på tredimensionell dataanalys inom medicinsk teknik samt traditionella bildanalysmetoder som nu anpassas till processindustrin.
Samma teknik vill också gruvföretaget Boliden använda för att mäta sin malm innan den krossas. Storleken på stenbitarna påverkar hur kvarnens hastighet och effektbehov ska styras. I dag har man bara en tvådimensionell bild.
I processautomation gäller det att ha grundläggande kunskap om kemi, material och vad som händer. Den kunskapen använder man för att bygga teoretiska modeller och finna bra regler för hur processen ska styras. Sedan måste man som sagt mäta inne i processen för att ge modellerna och reglerna aktuell information, och till sist styra processen.
Helst ska förstås allt detta ske automatiskt med hjälp av datorer.
– Vi har varit så fokuserade på kontorsautomation, men det är i processen man verkligen kan tjäna pengar på IT, säger Per-Olof Samskog.