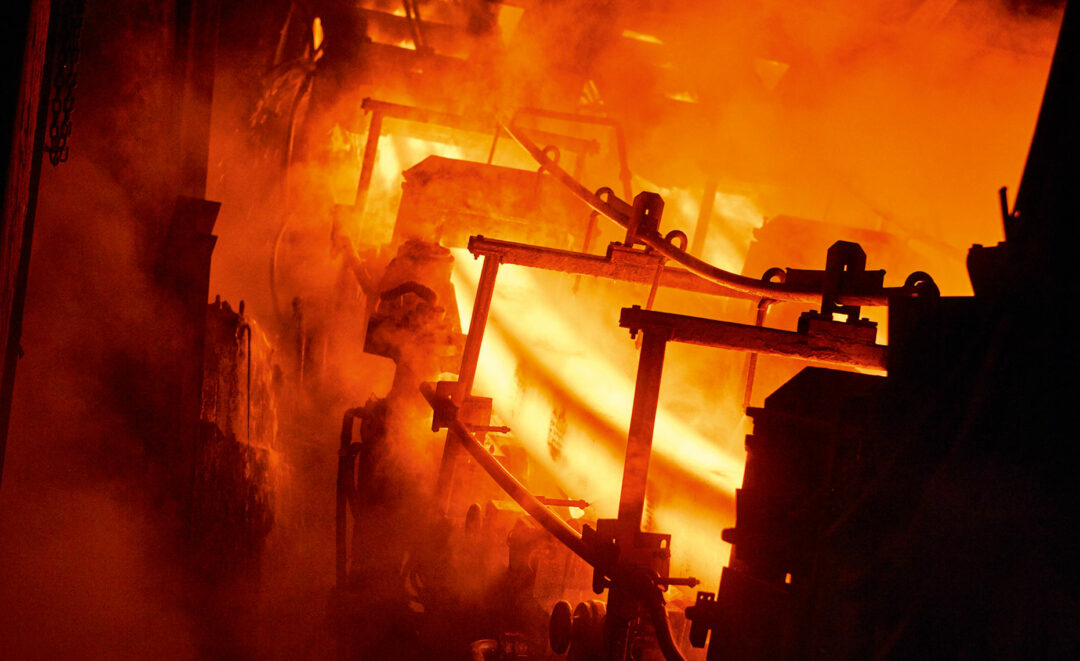
Bild: Pia & Hans Nordlander
Svensk klimatbov tämjs med vätgas
Dagens ståltillverkning kräver kol och står för 10 procent av Sveriges koldioxidutsläpp. Genom att byta ut kolet i processen mot vätgas kan utsläppen förvandlas till vatten. Men är det praktiskt möjligt?
”Det är stort, gigantiskt. Hela det moderna samhället bygger på storskalig järnframställning, och kol är en absolut nödvändig del av processen. För att byta ut kolet måste vi bygga upp ett i grunden nytt system.”
Martin Pei har arbetat länge inom den svenska stålindustrin. Han har en doktorsexamen i metallurgi vid Kungliga tekniska högskolan och leder sedan tre år tillbaka teknikutvecklingen på stålföretaget SSAB. Ändå har han svårt att hitta de rätta orden för att beskriva omfattningen av det senaste projektet. Det går ut på att stöpa om en av världens äldsta industriprocesser, masugnen. Målet är att utveckla en ny typ av ugn, som matas med vätgas i stället för kol och som släpper ut vatten i stället för koldioxid. Om det lyckas kan Sverige bli först i världen med att tillverka fossilfritt stål.
Bakom projektet, som kallas Hybrit, står SSAB tillsammans med gruvkoncernen LKAB och energibolaget Vattenfall. De första planerna började smidas för två år sedan. Nu har de tre företagen bildat ett gemensamt bolag för att gå från ord till handling, med Martin Pei som ordförande.
Under årens lopp har stålindustrin gjort mycket för att minska energianvändningen och därmed utsläppen. Rökgaserna återanvänds så långt det är möjligt inom stålverket. Spillvärmen blir dessutom fjärrvärme i det omgivande samhället.
Enligt Martin Pei finns det inte mycket kvar att skruva på i processen.
– I dag ligger vi väldigt nära den teoretiska minimigränsen för kolförbrukningen, säger han.
Trots det står stålindustrin för en tiondel av de svenska koldioxidutsläppen. Och den svenska riksdagen har slagit fast att Sverige ska bli koldioxidneutralt till 2045.
– Det kräver att vi får bort problemet vid källan, i masugnen. Vi kan inte fortsätta att importera kol, säger Martin Pei.
Masugnen med sin långa historia är fortfarande hjärtat i ståltillverkningen. Den äldsta masugnen i Sverige – och Europa – har hittats i Norberg i Bergslagen och är från 1100-talet.
Uppgiften är – nu som då – att få fram rent järn genom att ta bort det syre som är bundet i järnmalmen. Till det används kol i form av koks, som reagerar med syret vid hög temperatur. Då bildas koldioxid. Efter denna så kallade reduktion kan det rena järnet rinna ut i botten på masugnen, medan koldioxiden till slut försvinner upp i atmosfären efter att värmen har tagits om hand.

Till vänster: Dagens masugn kräver kol.
Till höger: Framtidens masugn använder vätgas.
Bild: Johan Jarnestad
I Hybrit ska kolet ersättas med vätgas. Finessen är att det då inte bildas någon koldioxid vid reduktionen av järnmalmen. Vätet reagerar med syre och bildar i stället vatten. På pappret är det en enkel lösning som även har bevisats genom experiment och teoretiska beräkningar.
Men i praktiken är det en annan femma. Att använda vätgas i industriprocesser är i och för sig ingenting nytt, men det mesta av dagens vätgas tillverkas av fossil naturgas. För att bli fossilfri ska den i stället tillverkas av vatten, som genom elektrolys spjälkas till vätgas och syrgas med hjälp av grön el. Haken är att tekniken fortfarande är dyr och bara används i förhållandevis liten skala.
Mikael Nordlander är forskningsansvarig för framtidens energisystem på Vattenfall och leder arbetet med att se över möjligheterna till storskalig tillverkning och lagring av vätgas i Sverige. Hittills har han och ingenjörerna på Vattenfall inte stött på några tekniska hinder, även om det handlar om mycket stora volymer vätgas.
– Jag brukar jämföra med Globen-arenan i Stockholm. Om man inte trycksätter vätgasen behövs det en volym motsvarande Globen var tredje timme för att försörja en normalstor masugn som den i Luleå.
För att tillverka så mycket vätgas går det åt stora mängder el. Tillsammans med uppvärmning av processerna i ståltillverkningen handlar det om 15–20 TWh per år. Som jämförelse använde vi i Sverige totalt 140 TWh förra året. Att förse stålindustrin med el innebär en ökning med drygt 10 procent. Eller, för att ta en annan jämförelse, förra året producerade Sveriges 3 300 vindkraftverk tillsammans 15 TWh. Det skulle alltså behövas minst dubbelt så många vindkraftverk i Sverige bara för att kunna tillverka fossilfritt stål.
– Det är väldigt stora mängder el. Men vi har å andra sidan ett starkt och i princip utsläppsfritt elsystem i Sverige som ger ett årligt överskott, och utbyggnaden av förnybar el har inte slagit i taket, säger Mikael Nordlander.
Han menar att det är bättre att använda överskottet på hemmaplan för att ställa om industrin än att exportera el.
En annan stor utmaning är att reduktionen med vätgas kräver en ny typ av ugn som jobbar vid en lägre temperatur än den traditionella masugnen. Syret släpper från järnet och bildar vatten med vätgas vid ungefär 900 grader Celsius. Järnet är då fortfarande i fast form och kommer ut ur ugnen i små porösa klumpar, så kallad järnsvamp.
Järnsvampen måste genast tas om hand i elektriska stålugnar för att inte börja reagera med syre på nytt. Ska den mellanlagras krävs ytterligare ett steg, där järnsvampen bildar briketter.
– Det är många tekniska problem som måste lösas. Det är en sak att testa några gram järnoxid i ett laboratorium. Att åstadkomma en industriellt gångbar process är något helt annat, säger Martin Pei.
De första forskningsprojekten håller precis på att rulla i gång. Om allt går som planerat, ska en pilotanläggning finnas på plats någon gång runt år 2020. Sedan följer flera år av försök och först 2035 kan en anläggning i stor skala stå klar.
Projektet har hittills en budget på 114 miljoner kronor, varav ungefär hälften i form av bidrag. Men både stat och företag kommer att behöva skjuta till mer pengar. Bara bygget av pilotanläggningen kommer, enligt konsortiets beräkningar, att kosta omkring två miljarder kronor. Att regeringen i höstbudgeten lovar ett stöd på 300 miljoner kronor om året fram till 2040, för att industrin ska kunna minska utsläppen från sina processer, välkomnas därför.
I Sverige finns i dag tre masugnar: två mindre i Oxelösund och en stor i Luleå. Alla tre drivs av SSAB. Att bygga om dem i grunden påverkar inte bara företaget, utan också samhället runt omkring, eftersom spillvärmen värmer upp bostäder via fjärrvärme i dag.
Och även om kolet i masugnen byts ut mot vätgas finns andra utsläppskällor på vägen mellan gruvan och färdig produkt.
En sådan är de pelletsverk där den malda och anrikade malmen blandas med tillsatsämnen och bakas till små kulor, som masugnen sedan matas med. I dag eldas de svenska pelletsverken med olja och kol.
– Det är delar som vi också jobbar med inom Hybrit, säger Åsa Sundqvist, direktör för teknik- och processutveckling på LKAB.
Det är inte bara i Sverige som stålföretag satsar på vätgas. I Österrike planeras en stor elektrolysanläggning inom ramen för ett nytt EU-projekt. Även i Japan pågår utveckling av tekniken.
Parallellt utforskas också andra spår för att minska utsläppen av koldioxid vid stålframställning. Ett är att fånga in koldioxiden (se text här intill), ett annat att byta ut fossilt kol mot biokol. Ett tredje, mer drastiskt spår, är att smälta järnmalm med hjälp av elektricitet.
Några av de här lösningarna kan bli steg på vägen mot en helt fossilfri stålindustri, som ju är Hybrits slutmål.
– Det gör det så spännande, att vi faktiskt försöker gå till botten med själva rot-orsaken till koldioxidutsläppen, säger Åsa Sundqvist.
Samtidigt betonar hon riskerna och ser den långa tidshorisonten som en utmaning i sig.
– Det kommer att ta lång tid, vi talar decennier. Men någon gång måste man våga ta steget. Funkar det inte ska ingen kunna säga att vi inte försökte, säger Åsa Sundqvist.
Utsläpp från masugn blir fartygsbränsle
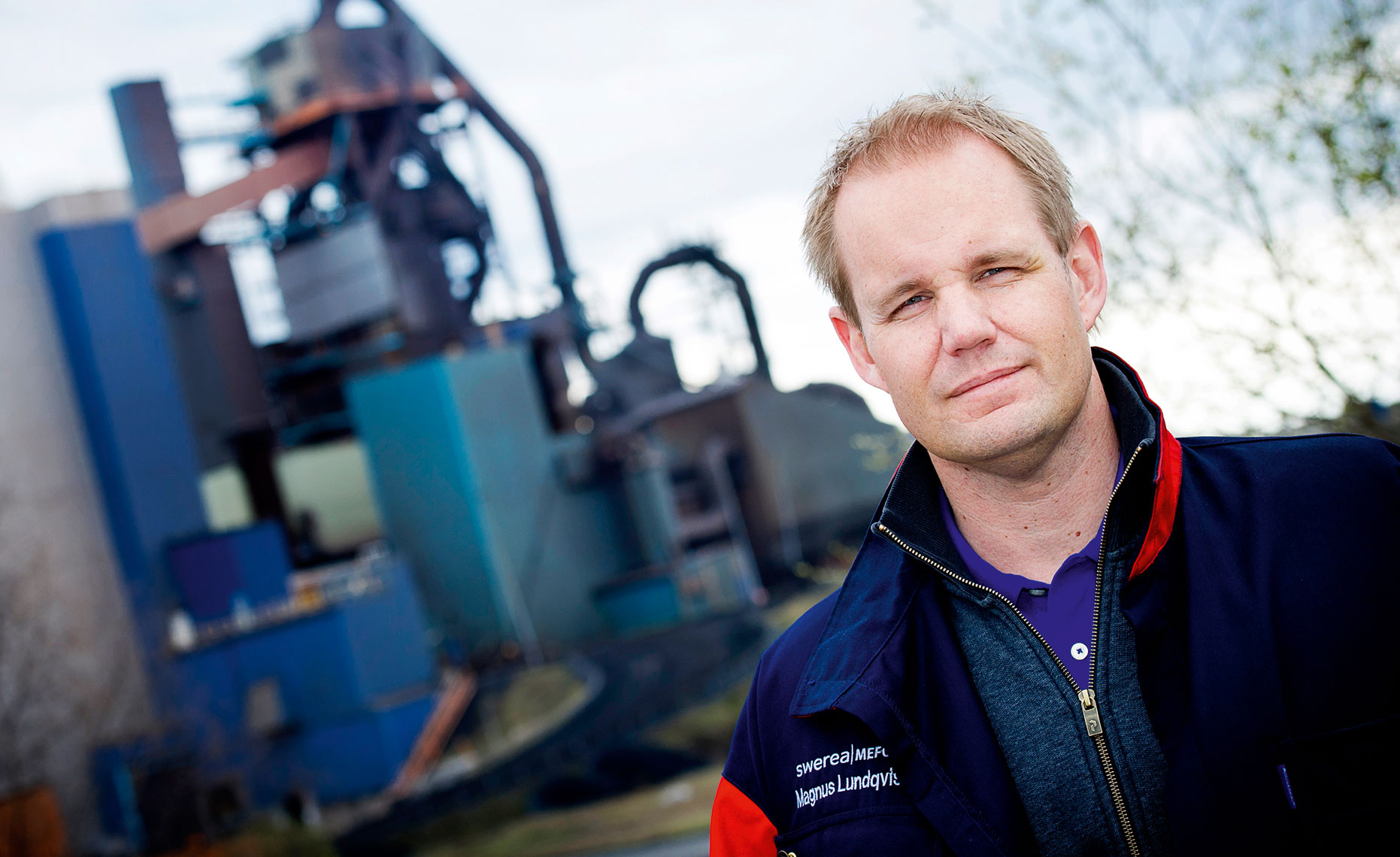
Vätgas är inte enda sättet att minska koldioxidutsläppen i stålindustrin. I Luleå ska gasen från masugnen förvandlas till metanol som ska driva fartyg.
Restgaserna från masugnen innehåller stora mängder koldioxid, men även kolmonoxid, vätgas och kvävgas. I dag används gaserna för el- och värmeproduktion.
– Nu vill vi använda gasen inte bara till värme utan också för att tillverka bränsle, säger Magnus Lundqvist, på forskningsinstitutet Swerea Mefos i Luleå.
Där leder han två EU-projekt som går ut på att skilja ut koldioxiden ur masugnsgasen och omvandla den till metanol.
En pilotanläggning för att skilja ut koldioxiden har just invigts och de första försöken sker under oktober. Restgaserna som används kommer från SSAB:s stora masugn via en 640 meter lång ledning. Tekniken är utvecklad i Nederländerna och bygger på ett katalytiskt material, som omvandlar masugnsgasen till vätgas och samtidigt fångar in koldioxiden.
– Det nya är att de två processerna sker samtidigt och bara kräver hälften så mycket energi som dagens bästa teknik för att fånga in koldioxid. Det gör att det också blir billigare, säger Magnus Lundqvist.
Vätgasen samlas in för sig och kan sedan användas för att tillsammans med koldioxiden bilda metanol. Den extra vätgas som behövs ska tillverkas med hjälp av elektrolys, precis som i Hybrit-projektet (som beskrivs här intill).
Den första metanolen ska börja tillverkas under nästa år. En av utmaningarna är enligt Magnus Lundqvist att masugnsgasen även innehåller små föroreningar som kan påverka processen.
Flera stålbolag, bland annat i Tyskland, utvecklar teknik för att fånga in och använda koldioxid som ett sätt att minska sina utsläpp.
Koldioxiden kan även lagras i marken. Det första stålverket i världen som fångar in och lagrar koldioxid finns i Förenade Arabemiraten, där koldioxid från ståltillverkningen pumpas ner i ett oljefält.